患者さんに安心して届けられる薬を製造する使命。そのために、どんな小さなミスでも誠実に報告し合い、改善を重ねる。
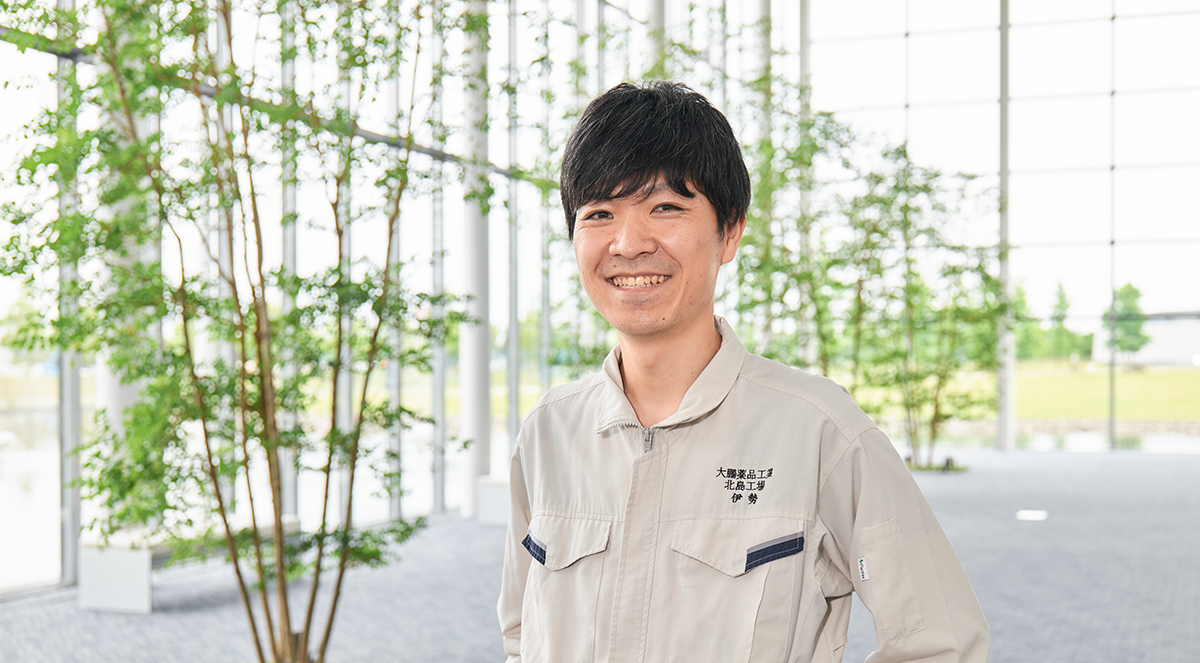
伊勢祐矢 (生産本部 北島工場 製造課)
抗がん剤に特化したグローバル生産拠点の北島工場
――生産本部とはどのような部署なのでしょうか。
大鵬薬品の生産本部には、徳島工場、北島工場(徳島県)、埼玉工場、犬山工場(愛知県)、計4つの工場があります。そして、これらの工場すべてに関わる品質管理部門があり、各工場を連携させながら、生産工程や試験工程の最適化を図り、厳しい品質管理基準のもと、医療用医薬品、医薬部外品などを製造しています。また、各工場に関わる間接部門として、設備技術部門、生産技術部門、生産管理部門の3つがあります。設備技術部門はインフラや設備機器の導入からメンテナンスを、生産技術部門は研究所で開発された原薬や製剤を工場で恒常的に生産する製造方法の検討を、そして生産管理部門は生産本部の中長期の基本方針の立案や本社と生産本部をつなぎ国内外への安定供給のための調整役などを担っています。
――その中で伊勢さんが所属する北島工場はどんなところなのでしょうか。
大鵬グループの抗がん剤を製造するグローバル生産拠点です。4つの工場の中では最も新しく、2013年の竣工です。
現在私は北島工場の製造課に所属しています。製造課では、抗がん剤を製造・包装して国内外へ出荷する際のスケジュール管理や実際の製造・包装などを担当しています。製造課に配属になって約3年間は包装工程に従事していましたが、2019年からは役割が変わり、製造作業者が集中かつ安心して作業ができるようサポートするのが私の業務になりました。
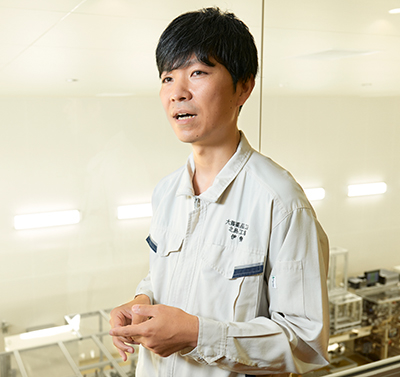
医薬品を製造する際、GMP※1という省令を遵守する必要があります。この省令では生産活動における必要な手続きや、とるべきアクションが規定されています。GMPに則り必要なプロセスが正しく漏れなく行われているかを逐次確認するのも私の大事な仕事です。
例えば、ある薬の製造手順を少し変えたい、原料の購入元を変更したいという場合、バリデーション※2という検証業務を行うことが義務づけられています。これは、変更に伴うリスクを洗い出した上で、同じ品質の製品を製造できるかを検証する作業です。バリデーションを行うには、GMP省令に基づいて、医薬品や原材料、製造工程を記載した文書を作成し保管する必要があるのですが、私はバリデーションにおける製造課内の担当責任者も兼ねています。
また、製薬会社の工場は医薬品規制当局による査察があります。北島工場にも徳島県、PMDA※3、さらに海外展開していることからアメリカの政府機関であるFDA※4の査察など海外の規制当局の査察を定期的に受けています。そうした査察の関係者が来られた時も、主メンバーとして対応を任されています。その際の業務を一言で言えば、過去から現在にかけて行ってきた製造管理および品質管理を説明する、なのですが、査察に適合しなければ患者さんに医薬品をお届けできなくなるので、毎回緊張します。
※1 GMP:Good Manufacturing Practiceの略称。医薬品および医薬部外品の製造および品質に関する世界基準。品質の良い医薬品を安定して製造するための製造管理・品質管理の基準をまとめたもの。
※2 バリデーション:製造所の構造設備ならびに手順、工程その他の製造管理および品質管理の方法が期待される結果を与える事を検証し、これを文書とすることによって、目的とする品質に適合する製品を恒常的に製造できるようにすることを目的とする。
※3 PMDA(Pharmaceuticals and Medical Devices Agency): 独立行政法人 医薬品医療機器総合機構の略称
※4 FDA:Food and Drug Administrationの略称。アメリカ食品医薬品局のことで、食品や医薬品を取り締まるアメリカ合衆国の政府機関。日本の厚生労働省のような役割を担っている。
さまざまな科学的データの上で成り立つ、医薬品の「製造」
――いろいろ責任のある仕事を任されているのですね。
そうですね。結構早い段階から任せてもらっています。入社した2005年当時まだ北島工場はなく、私は徳島工場工務課の配属でした。1年目は機械の点検や修理担当だったのですが、2年目から業務が一転、設備の改造や更新、徳島工場内に新設する工場の建設に関わる業務、設備の予算管理など管理業務を担当するようになりました。
その後、さまざまなプロジェクトにリーダー、副リーダーとして関わるなど、次々に責任ある仕事を任せてもらっています。苦しい局面もありましたが、課題に向き合うことで成長すると考えているので、常に楽しいですね。
――医薬品を扱う工場ならではの大変さもあると思うのですが。
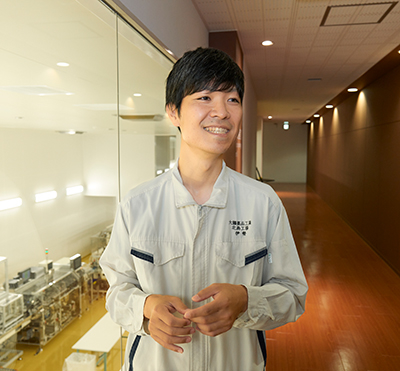
医薬品でなくとも工場に新しい設備を導入すれば、必ず試運転をするはずです。それで問題なければ、製品を作ることができると思います。ただし、薬は外観だけでは品質の良否を判断できず、科学的に保証されていなければなりません。そのため、先ほどお伝えしたようにGMP省令の定める製造管理・品質管理の基準を満たしていることを製造過程の一つ一つにおいて検証し、文書化する必要があります。これが薬の製造工場の特徴的なところですが、全ては患者さんに安心してお届けできる製品にするために必要なことです。
――北島工場で実際に製造する人たちをサポートするうえで心がけていることは?
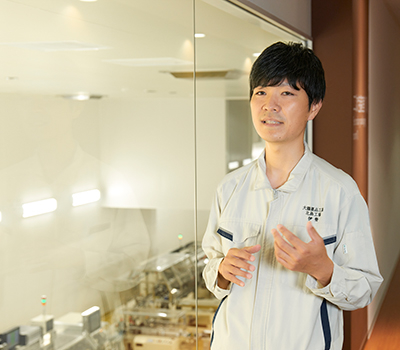
GMPの原則の一つに「人為的なミスを最小限にすること」があります。私たちの生産現場においても小さな人為的なミスは発生し得ます。それは許されないことではあるのですが、人為的なミスを検出する仕組み作りはもちろんのこと、ミスをしてしまったら本人がすぐにミスをしたと誠実に言えること、また報告できる雰囲気作りが何より大事です。特に工場は、開発から薬ができるまでのすべてのデータを集約した製品を世に送り出す最後の工程です。この次には、その薬は医師と薬剤師を通して患者さんの手に直接渡ります。ですから、品質が適切でない製品が患者さんに届いてしまうことを絶対に阻止するという点から、仕事に対して誠実でまじめというのは外せない要素です。
だからこそ、些細なミスをしても隠さないで話してもらえるような環境づくりをサポート担当として心がけています。
ミスをした後も重要です。例えば、ボタンを押し間違えて錠剤がこぼれ落ちてしまったとします。そこで、「ボタンを押し間違えたAさんが悪い」とその人を責めても何の解決にもなりません。なぜそのボタンを押すことになったのか、何かの作業と並行していたからなのか、間違えやすい位置にボタンがあったからなのか、その原因を探り、その間違いが再度起こらないように改善を積み上げていくことの方が、薬の品質を安定させるためには大事です。そのことを常に肝に銘じていますね。
よりよい薬をより早く患者さんに届けられるよう、日々研鑽を積む。
――では、大鵬薬品のスローガン「いつもを、いつまでも。」を伊勢さんはどのようにとらえていますか。
患者さんの「いつもを、いつまでも。」を実現するために生産本部として考え、実行すべきことが2つあると思っています。一つは、「変わらないいつも」を守ることです。GMPを遵守した作業をいつも意識して作業しなければなりません。もう1つは「変えるいつも」です。物事に疑問をもって、いつもの中で出た課題を現場力で変えていくことで価値を生み出すことが必要です。
新薬は世に出るまで何年~何十年もかかります。その後、製造に携わる私たちが頑張って、滞りなく薬を届け続ける。場合によってはその期間を少しでも短縮し、その結果、少しでも早く、よりよい薬を患者さんにお届けできるかもしれない。そういうことを意識して日々のルーティンを粛々と責任を持って行い、かつ常によりよい方法がないかと研鑽を積む。それが私たちの責務だと思っています。
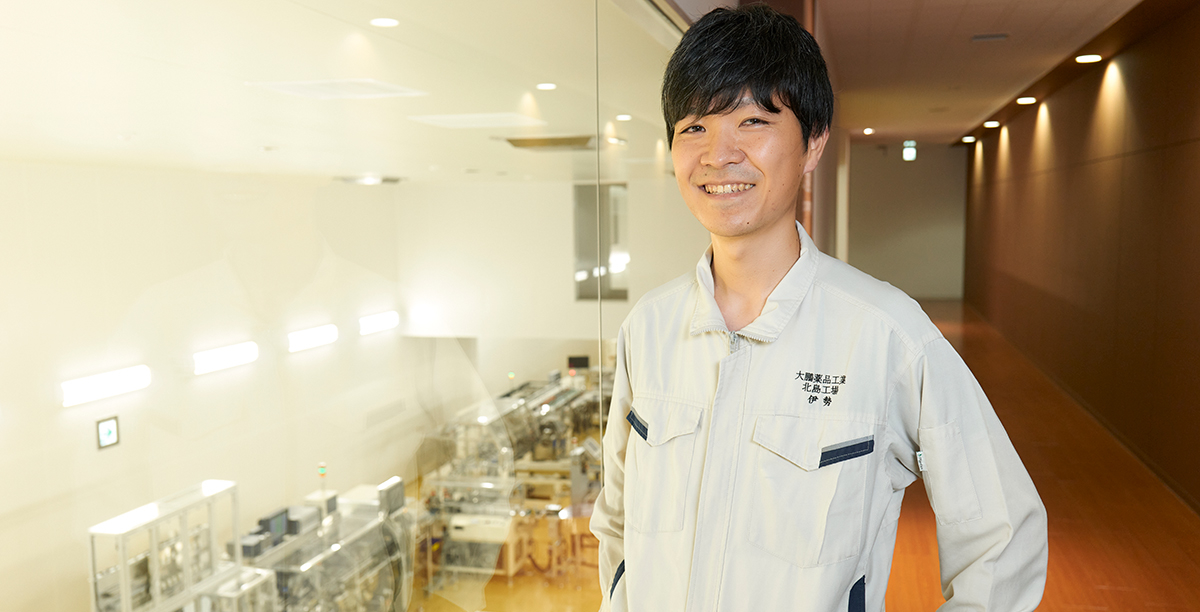
――今回、「いつもを、いつまでも。」を改めて考えたことで感じたことを最後に教えてください。
実はこのスローガンを、ここまで深掘りして自分で内省し考えたことはありませんでした。でも、じっくり考えてみたところ、私が「いつも」気持ちよく仕事ができているのは、多くの人たちに支えられている部分があるからだという気づきがありました。
みんなをサポートする立場でありながら、実は私の「いつも」は周りからのサポートによって成り立っている。これからはそれを常に意識しながら、職場のみんなと互いに支え合えるようになりたい。それが、最終的には私たちの仕事の先にある、患者さんの「いつも」を「いつまでも」実現することにつながるのかなと考えています。